The working world is experiencing enormous change at the moment. Production and manufacturing processes will also look different in the future. Above all, the topic of automation is of great importance – in the STIHL Group too. At several STIHL manufacturing companies around the world, our human colleagues now have real high-tech team members.
The STIHL Group is future-oriented in terms of its products and development, and not just when it comes to product design. In manufacturing too, STIHL is focusing on the future. The growing importance of battery-powered tools also involves new requirements for production processes and concepts such as automation, robotics, and artificial intelligence. Let’s take a look at the future of production at several STIHL companies around the world.
MODERNIZATION THROUGH INTELLIGENT HELPERS
People and robots – they could not be more different. But that difference is precisely what makes them a special team. The combination, which might at first glance seem incompatible, will create a community capable of shaping work processes better and more efficiently in the field of collaborative robotics. At the STIHL Group, a significant part of our sustainable alignment in manufacturing is achieved through investments in collaborative robotics. At several STIHL manufacturing companies, tremendous effort is being put into the implementation of “cobots” in manufacturing.
At the founding company, STIHL has been investing in this field and gradually expanding it since 2017: there are now seven cobots. The people and machines work together closely, which significantly eases the burden on employees in their day-to-day work. Monotonous and physically demanding tasks are being taken on by the robots, and the employees manage, control, and complete the tasks. Human intelligence, flexibility, and creativity are augmented by the precision, endurance, and power of the machines. A perfect combination.
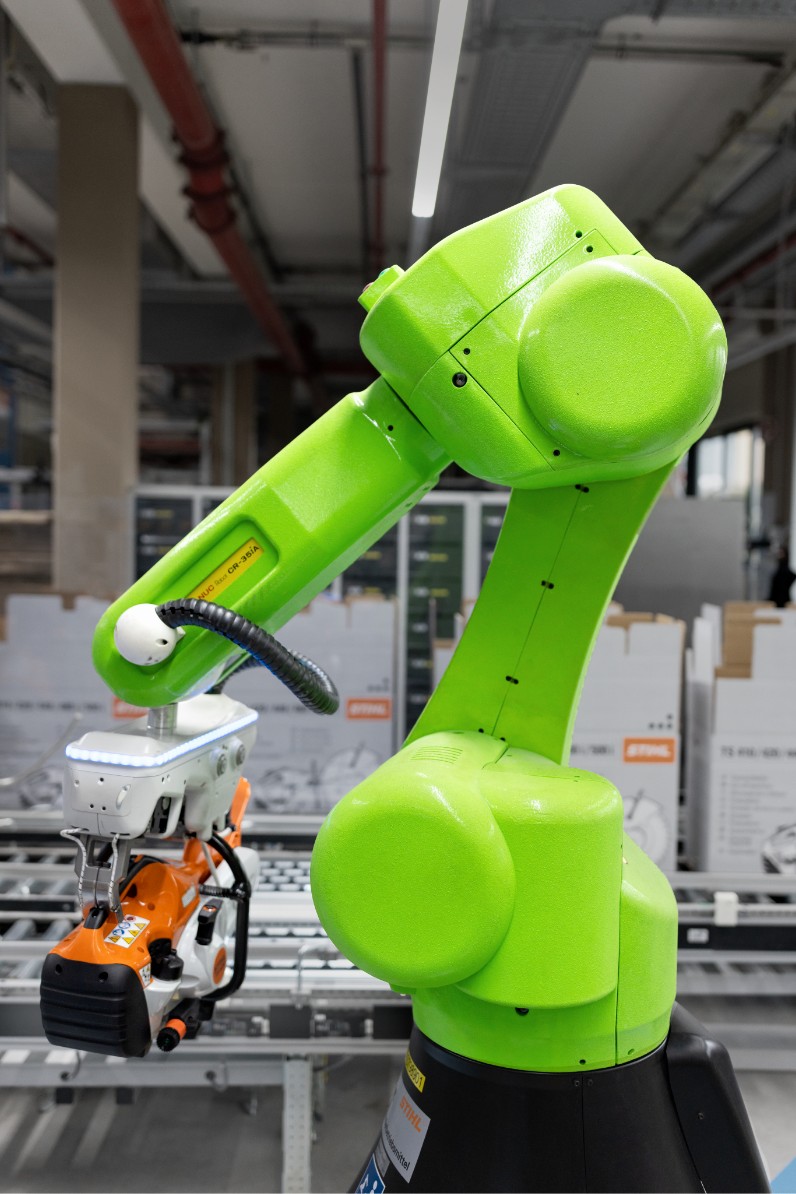
Co·bot
A cobot, also known as a co-robot or collaborative robot, is specifically designed to work with people. It does not work independently, but supports the machine operators in their work instead.
The five stages of
collaboration
safety barrier
The workspace of the robot is clearly defined by a barrier and mainly separated from that of the person. This means the employees are protected and the robot can work at optimum performance, specifically at high speed.
People and robots work without a safety barrier in their own workspaces. The robot uses sensors and scanners and is automatically stopped if employees enter its workspace.
cooperation
People and robots use a shared workspace, but different tasks within the process are worked on at different times. There is no direct interaction.
People and robots work side by side and at the same time in one workspace, but each on their own components. As in stage 3, complex safety mechanisms are installed to protect employees.
People and robots work hand in hand in a shared workspace. In addition to the safety mechanisms of stages 3 and 4, these robots have a sensitive outer layer that responds to contact and switches off the machines in the event of danger.
A NEW APPROACH WITH “HULK”
The first cobot implemented in the production process at STIHL was the lifting and packaging robot installed in 2017 by the manufacturer Fanuc, which is used on the cut-off machine line. The robot performs the “shake test” for the cut-off machine and the packaging process.
The launch of the lifting and packaging robot was something of a challenge for STIHL. Together with the robot manufacturer, the employer’s liability insurance association, and the relevant authorities, work processes were restructured, and new safety measures were developed before the cobots were integrated into work processes. Buying the robot is therefore not enough. Like human employees, a cobot must be trained. STIHL’s in-house tooling and equipment manufacturing conducts the complete integration of the cobot, including the construction of special parts, programming, and development of applications. This also ensures that our people can work safely with the robots while adhering to the highest level of safety and precautionary measures. The robots are equipped with sensors, which stop them when they come into contact with obstacles and protect against accidents between people and machines.
The robot has now become part of the team. Employees’ initial concerns about safety and working closely with the machine were quickly allayed. The intelligent colleague has now been fully accepted and even has a nickname: thanks to its power and bright green color, it is referred to as the Hulk. And the Hulk’s family is growing. Two additional computer-controlled lifting and packaging helpers arrived in 2021 to support the manufacture of STIHL professional blowers and chainsaws. Waldemar Eirich and Damir Uskok work together with the Hulks on a daily basis. “We initially had to get used to its speed, work steps, and our new roles in the collaboration. It was the first of its kind here,” adds Waldemar Eirich, looking back. Both sides have had to learn from each other. But now the team is “well coordinated.”
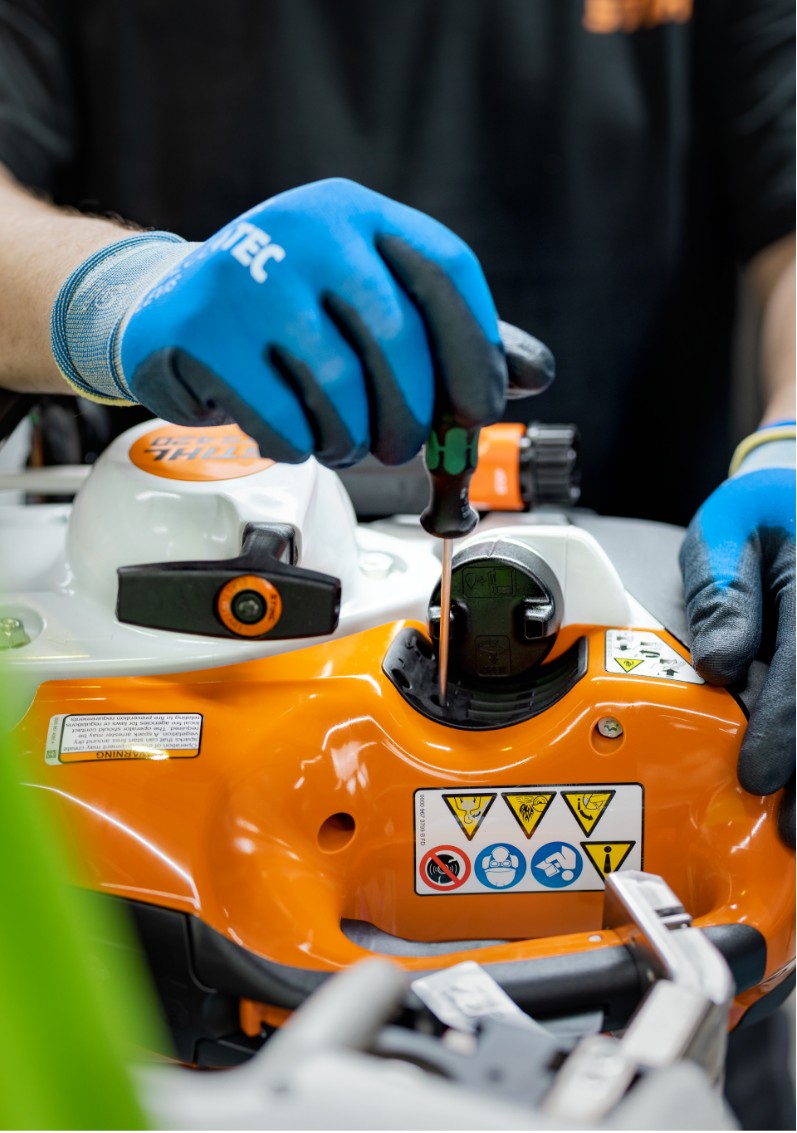
Lars Spittler, Senior Manager of the assembly center at the founding company in Waiblingen, provides an insight into the future use of cobots: “We see huge potential in the expansion of automated production processes and the use of collaborative robots. Production processes are becoming increasingly complex and the requirements of ergonomics in the workplace are higher.” Cobots will take over more and more of the burdensome tasks for people at STIHL in the future. People, in turn, are taking on the role of instructor and carrying out more of the preliminary work.
1518 times
per shift the collaborative robot “Hulk” lifts a cut-off machine. This saves the employees a total of
8 METRIC tons in weight
during an eight-hour shift.
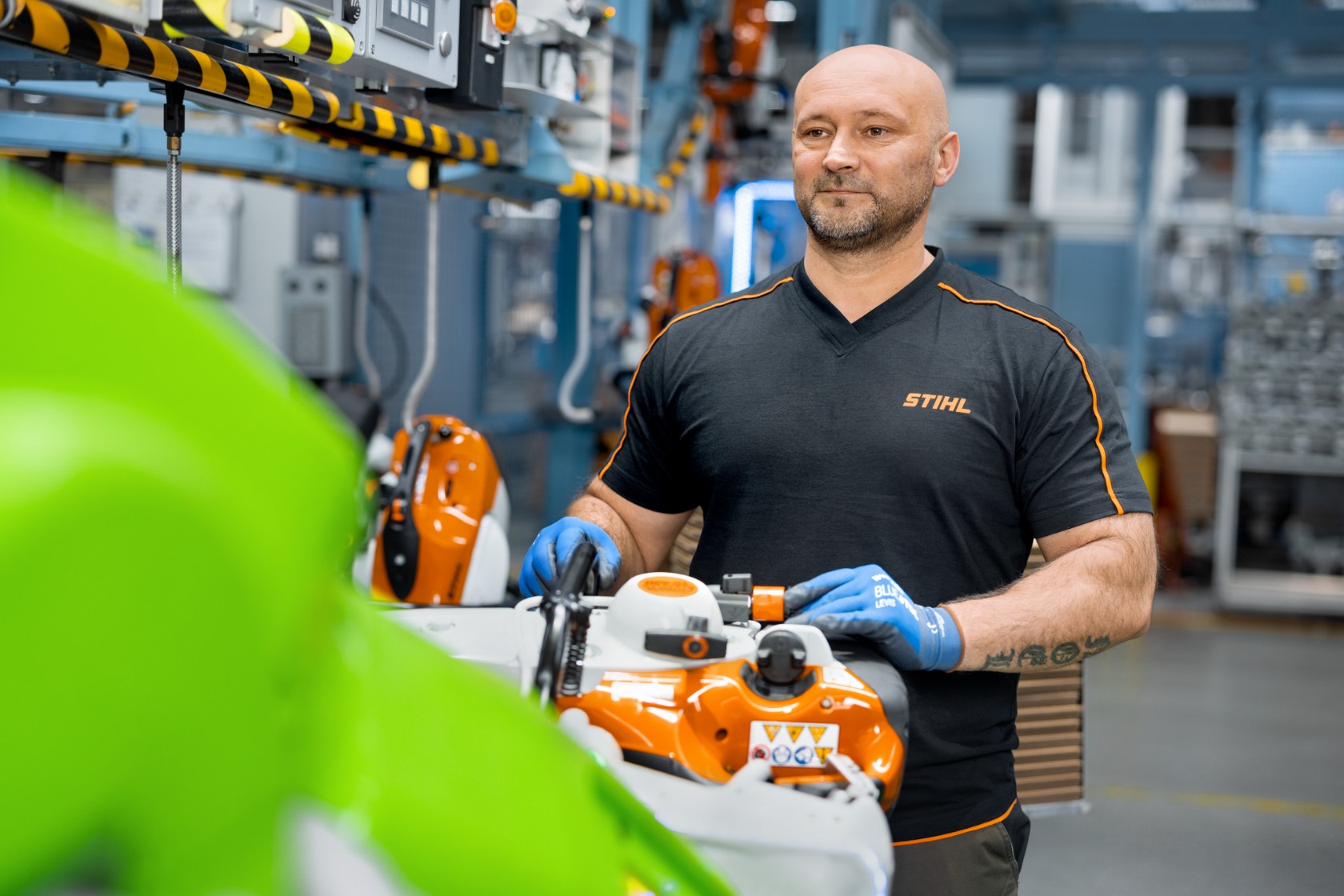
»Using the cobot makes my work less draining and more effective. We can now package considerably more products per shift.«
Production employee in Waiblingen
ROBOTS IN THE STIHL WORLD
The STIHL Group is also investing in intelligent helpers at other production companies in Austria, Brazil, and the USA.

Cobots @ STIHL Incorporated
»Our employees have confidence in the use of robots. Thanks to their intelligent functions and strict safety measures, cobots have been positively received.«
Director Manufacturing Engineering, STIHL Inc. (USA)
The STIHL plant in the U.S. is a trailblazer when it comes to collaborative robotics. The Virginia Beach production company has been investing in this technology since 2013 and now has nine active collaborative robots in assembly and plastics production. The project started with Universal Robots’ UR10 – at that time a real market innovation. At the beginning, however, there was considerable skepticism among the employees involved. But like in Waiblingen, doubts were quickly assuaged and today the cobot is a fully accepted member of the team.
The cobots actively work together with STIHL employees. One example of this is the robot that was commissioned in 2018 on a clearing saw line. The robot unloads the equipment and positions it for further processing. This saves its human team members the strenuous task of physical lifting and turning, reduces the work steps required, and minimizes the risk of injury.
Another robot was installed in 2021 for packaging blowers. Here, the use of machines significantly eases the physical burden on production employees.
The two cobots at STIHL Ferramentas Motorizadas in Brazil are brand-new. In 2022, both GoFa models from ABB Robotics were integrated into the existing production processes. They feature a built-in camera that checks finished chainsaws and clearing saws, thus ensuring the quality of the manufactured products before they leave the production line. If an error is detected, an employee will get involved and take over the rework where necessary.
The implementation of both robots was designed in cooperation with the production process engineers and implemented internally by the Automation Technology Department. What makes this special is that there are no boundaries or physical safety devices needed between the cobots and the employees. Both machines work safely side by side with their operators. The feedback has been absolutely positive – so positive, in fact, that two additional robots have already started working at the Brazilian assembly plant.
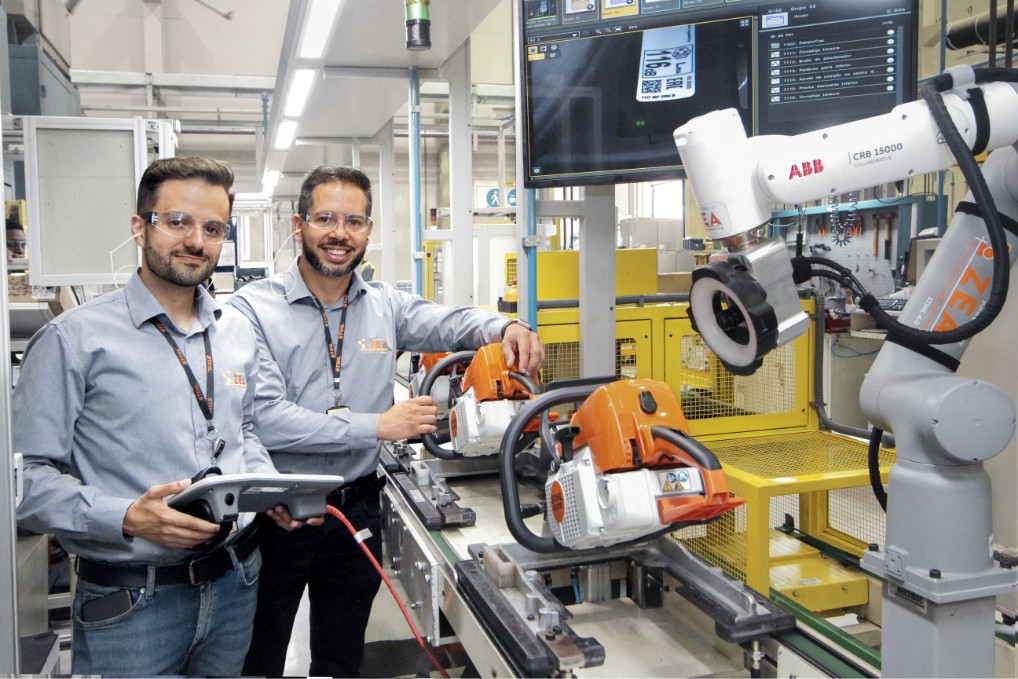
Cobots @ STIHL BRAZIL
AUTOMATION @ STIHL TIROL
At STIHL Tirol GmbH in Langkampfen, Austria, production processes are continuously being automated and modernized. One example is the assembly line for the STIHL HSA 60 and HSA 100, two next-generation battery-powered hedge trimmers. To meet market demand and STIHL’s high quality standards, many processes have been automated on this line, including the pressing process and the assembly of blades. Three robots in total demonstrate their skills in blade automation: “Sissi,” “Franz,” and “Seb.” In contrast to the machines at the founding company in Germany, STIHL Inc. in the U.S., and STIHL Brazil, Sissi, Seb, and Franz are screwdriving robots not cobots. They therefore work in a dedicated workspace with a safety barrier. Sissi, Seb, and Franz also actively support work on the line without direct interaction with employees.
Through automation, STIHL quality standards can be maintained in the manufacture of battery-powered hedge trimmers, production volume can be increased per work shift, and employees can be spared the most physically demanding work processes.
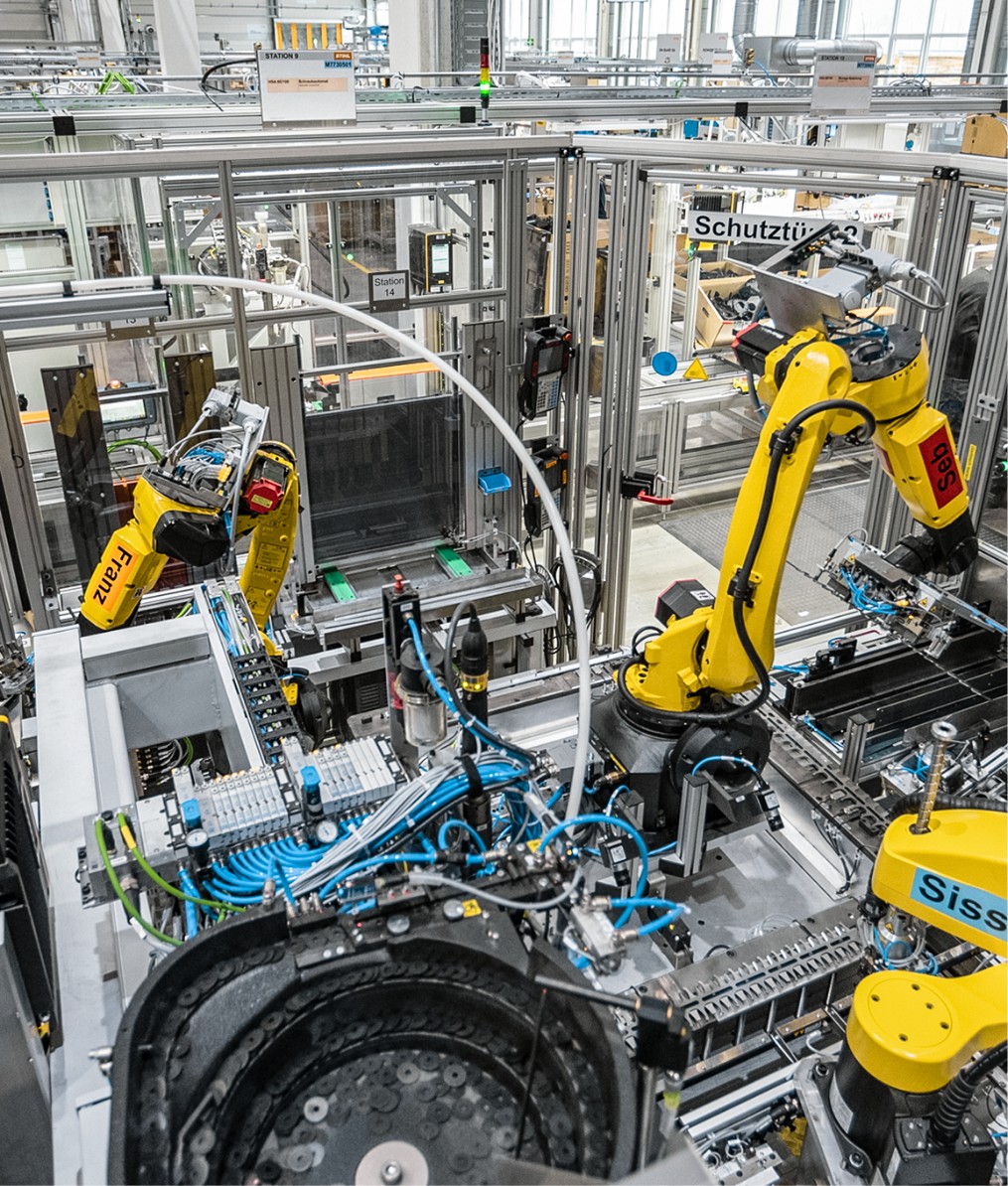